When evaluating moisture vs fire in construction, both pose serious threats—but fire demands immediate attention due to its life-threatening nature, while moisture causes gradual structural decay and health issues. The smartest approach is to use materials that address both risks. Products like moisture-resistant wall panels and fire-rated building materials—especially MGO panels—offer dual protection, making them ideal for modern, code-compliant buildings.
Introduction: Why This Question Matters in 2025
In 2025, construction professionals are navigating increasingly complex challenges—from climate change and regulatory shifts to rising client expectations for health, safety, and sustainability. One of the most critical debates in material selection today is moisture vs fire: which risk should be addressed first?
On one side, moisture is a silent, persistent intruder. It causes mold growth, weakens structural components, and damages interior finishes. On the other, fire is sudden and catastrophic—posing an immediate threat to life, property, and code compliance.
This decision isn’t just theoretical. It affects what types of moisture-resistant wall panels or fire-rated building materials you choose, how you prioritize budget, and where you allocate risk mitigation efforts in your project.
This article breaks down the impact of both threats, how building codes treat them, and why new-generation solutions like MGO panels are becoming the gold standard for tackling both simultaneously.
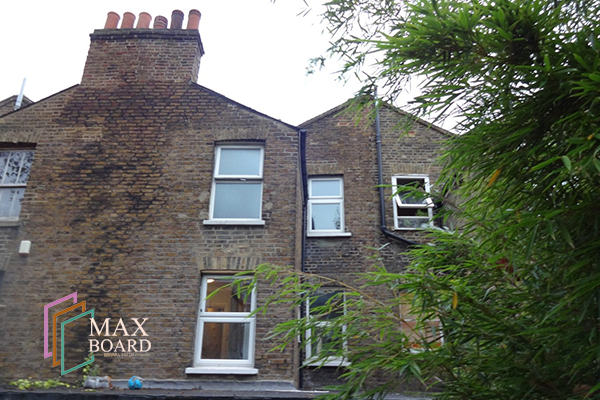
Understanding the Risk of Moisture in Buildings
Moisture may not spark headlines like fire, but it is one of the most common and costly threats to building health. It can enter through leaks, condensation, vapor diffusion, or improper insulation—and once inside, it spreads silently.
Unchecked moisture leads to:
- Mold and mildew, which degrade air quality and cause respiratory issues
- Decay of wood framing and corrosion of metal components
- Delamination and warping of wall finishes
- Increased energy consumption due to compromised insulation
Moisture damage also undermines long-term asset value. Renovating or restoring moisture-affected interiors is labor-intensive and expensive, often requiring the removal of entire wall systems.
This is why incorporating moisture-resistant wall panels is no longer optional in humid climates, wet areas (like bathrooms or basements), and in structures prone to condensation. Materials like MGO and MR boards offer superior protection due to their low water absorption, dimensional stability, and resistance to mold growth.
Ignoring moisture during the design stage invites years of hidden deterioration and escalating repair costs.
The Fire Threat: Immediate and Devastating
While moisture damage unfolds gradually, fire delivers destruction in seconds. In construction, fire is not just a design risk—it’s a life safety concern, governed by strict codes, insurance requirements, and material standards.
Fires in buildings can start from many sources:
- Electrical faults (overloaded circuits, faulty wiring, damaged devices)
- Cooking incidents or open flames
- Flammable materials (insulation, furniture, wall coverings)
- HVAC malfunctions or equipment failure
Once ignition occurs, the rate at which fire spreads depends almost entirely on material choice. Walls, ceilings, and finishes made from combustible materials accelerate flame propagation and smoke production—two of the primary causes of injury and death in structural fires.
The damage isn’t just physical:
- Loss of life and injuries
- Destruction of property and infrastructure
- Legal liability for non-compliance with fire safety codes
- Higher insurance premiums and denied claims
- Project shutdowns and delays
This is why modern building regulations demand the use of fire-rated building materials—those tested to withstand flames for 30, 60, or even 120 minutes under standards like ASTM E119 or EN 13501-1. These materials slow down heat transfer, block flame spread, and maintain structural integrity under extreme heat.
For example, fire-rated gypsum boards or MGO panels are designed to perform under such stress. They do not ignite, do not contribute to combustion, and provide critical time for evacuation and fire suppression systems to activate.
In fire-prone areas like stairwells, corridors, elevator shafts, and commercial kitchens, using non-rated materials is not just poor design—it’s legally negligent.
In the moisture vs fire debate, fire wins in terms of urgency and risk to life. Therefore, fire protection should be prioritized in areas where life safety is at stake—while also considering moisture where appropriate.
Comparing the Long-Term Damage of Moisture vs Fire
Deciding whether to prioritize moisture-resistant wall panels or fire-rated building materials ultimately depends on understanding how each threat affects a building over time.
Moisture Damage: Silent and Progressive
Moisture is insidious. Unlike fire, it rarely triggers alarms or evacuations. Its damage builds gradually, often undetected for months or years:
- Mold Proliferation
Damp drywall and untreated gypsum are breeding grounds for mold. Spores can travel through HVAC systems, spreading contamination throughout the building. This leads to chronic health complaints, from allergies to respiratory illness. - Structural Degradation
Moisture weakens adhesives, corrodes fasteners, and rots wooden framing. Over time, walls lose their load-bearing capacity, requiring expensive structural interventions. - Energy Inefficiency
Saturated insulation and wall systems lose their thermal performance. This forces HVAC equipment to work harder, spiking energy bills and operational costs. - Aesthetic Decline
Staining, bubbling paint, warped panels, and soft walls quickly diminish property value and occupant satisfaction.
Moisture rarely leads to total loss of the building, but it can erode profitability and health over decades if not addressed.
Fire Damage: Sudden and Total
Fire, in contrast, is catastrophic in minutes. One incident can undo years of investment:
- Complete Destruction
Combustible interiors can collapse, requiring demolition and total rebuilding. - Loss of Life
Fire claims thousands of lives each year globally, and lack of fire-rated building materials is often a factor. - Code Violations and Legal Liability
Buildings without proper fire-rated assemblies are subject to fines, lawsuits, or criminal charges. - Business Disruption
Even a small fire can shut down operations for months.
Balancing Both Risks
When comparing moisture vs fire, the distinction is clear:
- Moisture damages profitability, health, and long-term durability.
- Fire threatens immediate life safety, compliance, and total property loss.
This is why the smartest designers look for materials that address both. For example, MGO panels combine high moisture resistance and a Class A fire rating—allowing a single solution to mitigate both threats.
In 2025 and beyond, relying on products that solve only one problem often means exposing your project to the other.
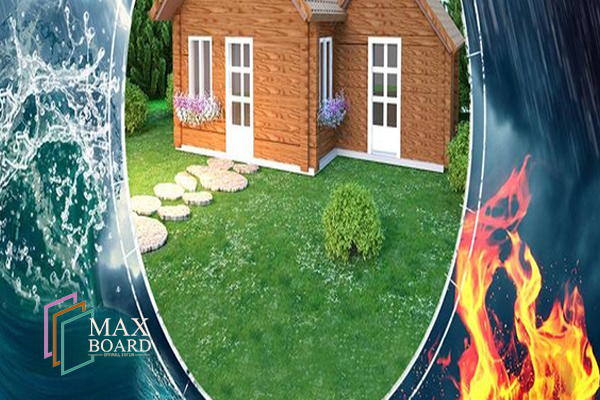
How Building Codes Prioritize Fire and Moisture Protection
When designing a structure, compliance with local and international building codes isn’t just a formality—it’s a legal, functional, and financial necessity. These codes define how and where fire-rated building materials and moisture-resistant wall panels should be used, and in which order of priority.
Fire Protection Takes Legal Precedence
In virtually all modern building codes—such as the International Building Code (IBC), National Fire Protection Association (NFPA) standards, and European EN standards—fire safety is treated as a top priority.
Why?
- Fire directly threatens life: Codes are built to ensure that people have time to evacuate before a fire spreads.
- Fire spreads fast: Flame, heat, and smoke can engulf a building in minutes.
- Insurance and liability: Fire compliance is often tied to insurability and the legal validity of a structure.
Examples of code requirements:
- Fire-rated assemblies in egress corridors and stairwells
- Fire-resistant materials in shafts and service risers
- Minimum fire resistance ratings (30, 60, 120 minutes) for walls and ceilings
Without certified fire-rated building materials, the structure may fail inspections, lose occupancy permits, or expose the owner to legal action.
Moisture Protection Is Performance-Based
Moisture control, while not always legally mandated in the same way as fire protection, is essential for long-term performance and indoor health. Codes such as ASHRAE 160 or certain sections of the IBC require vapor retarders, drainage planes, and moisture-resistant finishes in specific zones.
For example:
- Bathrooms, kitchens, and laundry rooms must use moisture-resistant wall panels
- Basements and exterior walls require water-resistant barriers
- Commercial kitchens may require washable and non-absorbent surfaces
Moisture protection is critical to energy efficiency, air quality, and durability—but it is usually enforced through performance standards rather than strict life-safety mandates.
How Codes Reflect the Moisture vs Fire Debate
In short:
- Fire protection is life-safety mandated and code-enforced
- Moisture protection is quality-of-life guided and code-supported
Designers and specifiers must satisfy both. Failing to meet fire code halts construction. Ignoring moisture leads to long-term failure.
This is why multipurpose solutions—such as MGO boards—are becoming more common. They check both boxes in one material, helping projects stay compliant and protected.
Material Science: What Panels Handle Both Risks?
As the construction industry moves toward smarter, safer, and more efficient design, the demand for materials that solve multiple problems is growing. For years, architects and builders had to choose between moisture-resistant wall panels and fire-rated building materials, often compromising on one risk to address the other.
But thanks to advances in material science, that tradeoff is no longer necessary.
Traditional Materials: One Strength, One Weakness
- Standard gypsum board is affordable and easy to install but absorbs moisture and has limited fire resistance unless specifically treated.
- MR (moisture-resistant) gypsum board resists humidity but still burns quickly if not combined with fire-retardant additives.
- Cement boards resist moisture and fire, but they’re heavy, hard to cut, and expensive to install.
- Plywood or wood panels are structurally strong but highly combustible and prone to mold.
These options force designers to layer solutions—using moisture-resistant panels on wet walls and fire-rated panels in egress zones, increasing cost, weight, and installation complexity.
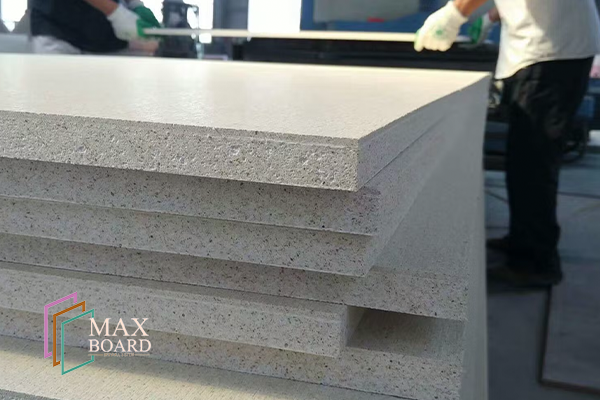
MGO Panels: The Dual-Protection Solution
Magnesium oxide (MGO) boards represent a breakthrough in panel technology. Engineered as both moisture-resistant wall panels and fire-rated building materials, they eliminate the need for compromise.
Key performance features include:
- Class A fire rating under ASTM E84 and EN 13501-1
- Low water absorption and resistance to mold and mildew
- Dimensionally stable, even after repeated exposure to moisture
- Non-combustible and non-toxic, ideal for health-sensitive spaces
- Compatible with paint, tile, cladding, or wallpaper
- Lightweight and easy to cut, making installation faster than cement board
Whether you’re building a commercial kitchen, hospital ward, luxury bathroom, or fire-rated hallway, MGO panels deliver what both performance and compliance demand.
By bridging the gap between moisture vs fire, MGO panels set a new standard for responsible, future-proof construction.
Where to Prioritize Moisture-Resistant Wall Panels
While all buildings are exposed to some level of humidity, certain spaces demand proactive moisture control due to their environmental conditions, daily use, or structural vulnerability. Choosing the right moisture-resistant wall panels for these zones helps prevent long-term damage and supports occupant health.
1. Bathrooms and Wet Areas
Showers, tubs, and sinks produce constant steam and splashing. Without proper moisture resistance, walls behind tiles or paint will absorb water, leading to swelling, delamination, and mold.
Solution: Use MR gypsum boards or MGO panels behind tiles and waterproof finishes.
2. Kitchens and Commercial Food Prep Zones
Cooking creates humidity, grease, and condensation. In commercial kitchens, this is amplified with industrial-scale appliances.
Solution: Use water-resistant panels that can handle vapor and be cleaned frequently without degrading.
3. Laundry Rooms and Utility Spaces
These zones often experience high ambient humidity, as well as leaks or hose ruptures. Standard drywall degrades quickly here.
Solution: Install moisture-resistant wall panels behind and around appliances and sinks.
4. Basements and Below-Grade Areas
Soil contact, poor ventilation, and cooler temperatures make basements highly susceptible to condensation and seepage. Wall cavities often trap vapor, allowing mold to grow undetected.
Solution: Use non-organic, low-absorption materials like MGO that are not affected by groundwater vapor or temperature shifts.
5. Exterior-Facing Walls in Humid Climates
In tropical or coastal regions, ambient humidity itself can seep into unprotected walls—even without direct water exposure.
Solution: Moisture-resistant sheathing and interior wall panels ensure continuous protection from both sides of the wall assembly.
Prioritizing moisture-resistant wall panels in these environments reduces the need for remediation, extends material lifespan, and keeps interiors safer and healthier.
Where to Use Fire-Rated Building Materials
Fire safety isn’t just about choosing the right materials—it’s about placing them in the right locations. Building codes around the world dictate where fire-rated building materials must be used, based on risk level, occupancy type, and evacuation needs. Misplacing or omitting fire-rated protection in these areas can have serious legal and safety consequences.
1. Egress Corridors and Exit Routes
These are the critical paths people rely on during emergencies. Any delay caused by smoke or flame spread could cost lives.
Requirement: Walls and ceilings must be built with materials that provide at least 1-hour fire resistance (e.g., ASTM E119–rated assemblies).
2. Stairwells and Elevator Shafts
Fire can travel vertically through buildings if these areas are unprotected. They must be sealed and reinforced with fire-rated materials.
Solution: Use MGO boards or fire-rated gypsum panels with sealed joints and tested framing assemblies.
3. Multi-Family and High-Rise Dwellings
Apartments and condominiums require fire separation between units to prevent horizontal flame spread and maintain compartmentalization.
Requirement: Use 1- to 2-hour fire-rated partitions between units and shared walls.
4. Commercial Kitchens and Utility Rooms
These areas contain heat-generating equipment, open flames, and electrical loads—all of which increase ignition risk.
Solution: Install fire-resistant panels on walls, ceilings, and around equipment, especially near exhaust systems.
5. Garages and Attached Structures
Many fire codes require fire separation between a residence and its garage, particularly when the garage houses fuel or combustion engines.
Solution: Use fire-rated wall and ceiling assemblies between the two spaces, even if the garage is detached.
6. Schools, Hospitals, and Public Buildings
In facilities with vulnerable populations or high occupancy, the consequences of fire are even more severe. Codes often require enhanced fire protection throughout the entire building envelope.
Solution: Use continuous fire-rated assemblies in corridors, patient rooms, classrooms, and mechanical shafts.
In short, fire-rated building materials must be strategically placed wherever human life, vertical travel, or fire spread potential is present. Compliance is not optional—it’s enforced by inspectors, demanded by insurers, and expected by users.
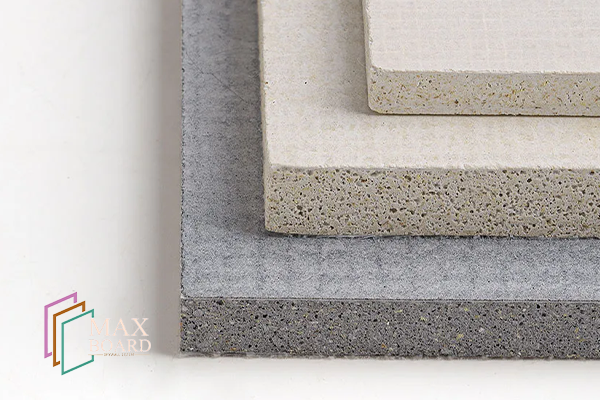
Why MGO Panels Offer the Best of Both Worlds
In the ongoing debate of moisture vs fire, most materials force builders to choose one strength at the expense of another. Traditional drywall swells in damp conditions. Cement board resists water but is heavy and brittle. Fire-resistant gypsum slows flames but often lacks mold protection.
That’s where MGO panels—magnesium oxide boards—stand apart.
1. Dual-Resistance Performance
MGO panels are inherently moisture-resistant wall panels and fire-rated building materials in one product. They resist water penetration, do not support mold growth, and carry Class A fire ratings under international standards (ASTM E84, EN 13501-1).
2. Non-Combustible and Non-Organic
Unlike traditional drywall or wood-based panels, MGO contains no cellulose or flammable additives. It does not burn, drip, or release toxic fumes during fire exposure. It also won’t rot, decay, or attract insects in humid environments.
3. Lightweight and Easy to Install
Compared to cement board, MGO is lighter, easier to cut, and less abrasive on tools. This reduces labor time and material waste during installation.
4. Compatibility with Finishes
MGO boards accept tile, paint, wallpaper, and cladding, making them versatile for aesthetic design without compromising on protection.
5. Sustainable and Low-VOC
MGO is produced with minimal emissions, often using recycled content. It supports green building certifications like LEED, WELL, and Estidama.
6. Ideal for High-Risk Zones
Because MGO handles both moisture and fire, it’s ideal for:
- Bathrooms and kitchens
- Corridors and stairwells
- Commercial kitchens and basements
- Schools and healthcare facilities
- Multi-unit residential buildings
In short, MGO panels eliminate the need to choose between moisture-resistant wall panels and fire-rated building materials. They deliver both in one smart, future-ready solution.
Conclusion: Don’t Choose Between Moisture and Fire—Protect Against Both
In today’s complex building environment, there’s no room for single-purpose solutions. Both moisture and fire pose real, costly risks—one creeping silently through humidity and condensation, the other striking suddenly with life-threatening force. The question is no longer moisture vs fire, but how to defend against both, intelligently and economically.
Traditional materials force compromise. But innovative options like MGO panels allow you to move forward without trade-offs—providing dual protection as both moisture-resistant wall panels and fire-rated building materials.
Whether you’re building a home, a hospital, or a high-rise, the safest, smartest path is to choose materials that anticipate both risks—because in construction, the cost of being unprepared is always higher.
Get Expert Help for Your Project
Ready to upgrade your building’s protection? Our team at MaxBoard can help you select the ideal panels based on your local climate, code requirements, and project timeline.
📞 Contact Us Now for a custom consultation, technical specifications, or bulk pricing.
MaxBoard MGO Panels — Built to resist what others can’t.